Robotic welding is at the forefront of modern technologies that have significantly transformed the metalworking sector. It provides a quick, fast, and dependable method of attaching metal components through the process of "welding." This innovative method involves programming robots to perform repeated operations, allowing them to outperform human welders in terms of speed and production. However, a thorough evaluation of the benefits and drawbacks of robotic welding is required to acquire a better understanding of its influence. Let's go into the details.
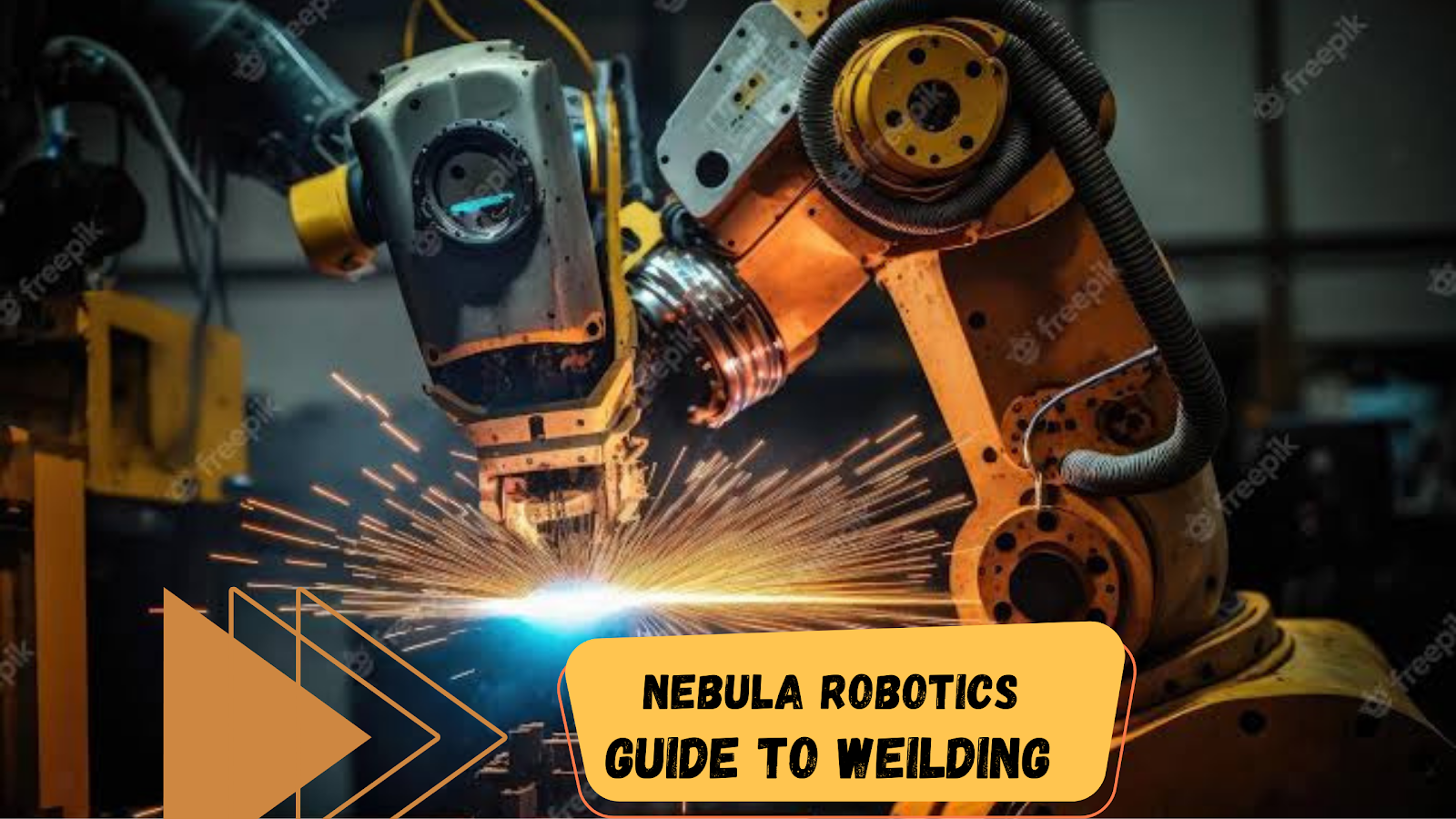
Click here to Discover Nebula’s Wielding Robots!
Wonders of Weilding
Robotic welding has several advantages over manual welding, making it a popular alternative in the metalworking industry:
- Enhanced Cost-Efficiency: Because robotic welding eliminates the need for human labor, it greatly decreases costs, especially in large-scale projects with extensive welding requirements.
- Precise and Consistent Performance: Because they can be programmed to produce welds with exact specifications, robotic welders demonstrate extraordinary precision and consistency in their work.
- Reduced Overall Costs: Robotic welding is more efficient than traditional methods, reducing material waste and reducing the need for rework and repairs, resulting in lower overall costs.
- Weld Quality is Improved: The uniformity given by robotic welders provides improved weld quality, reducing the chance of flaws that may occur with human welders.
- Increased Productivity: Because robots are indestructible, they can operate constantly and at a faster rate than manual welders, resulting in increased productivity.

Woes of Wielding
Despite the obvious benefits of robotic welding, it does have some limitations that must be considered:
- Large Initial Cost and Time-consuming Setup: The large initial investment necessary for setting up robotic welding systems is a key disadvantage. The cost can be significant, making it less cost-effective for smaller-scale projects requiring only a few number of welds. Furthermore, the setup process might be time-consuming, adding to the initial costs.
- Limited Error Detection Capability: Without close supervision by an experienced welder, robots may not always detect welding process problems, such as improper connections. This lack of real-time mistake detection could result in erroneous or faulty welds, thereby impacting overall work quality.
- Inflexibility in Applications: Once programmed for a certain application, robotic welding systems can be rigid. It can be difficult to change them to accommodate changing materials or joint types, making it less ideal for projects involving multiple types of welds.
- Welding Positions: The number of welding positions that robotic welding systems can handle is limited. They are generally intended for flat or horizontal welding locations, which limits their capabilities when working with pieces with irregular shapes or that require non-standard welding angles.
- Knowledge of specialized programming is required: Operating robotic welding systems efficiently necessitates specific programming knowledge, which can make it difficult for businesses to locate experienced operators. Errors in programming can result in poor weld quality or possibly dangerous conditions.
- Potential Safety Hazards: If not used properly, robotic welding systems might be hazardous to operators. Arc flashes and welding gases can be hazardous to an operator's health if proper safety equipment and procedures are not used.
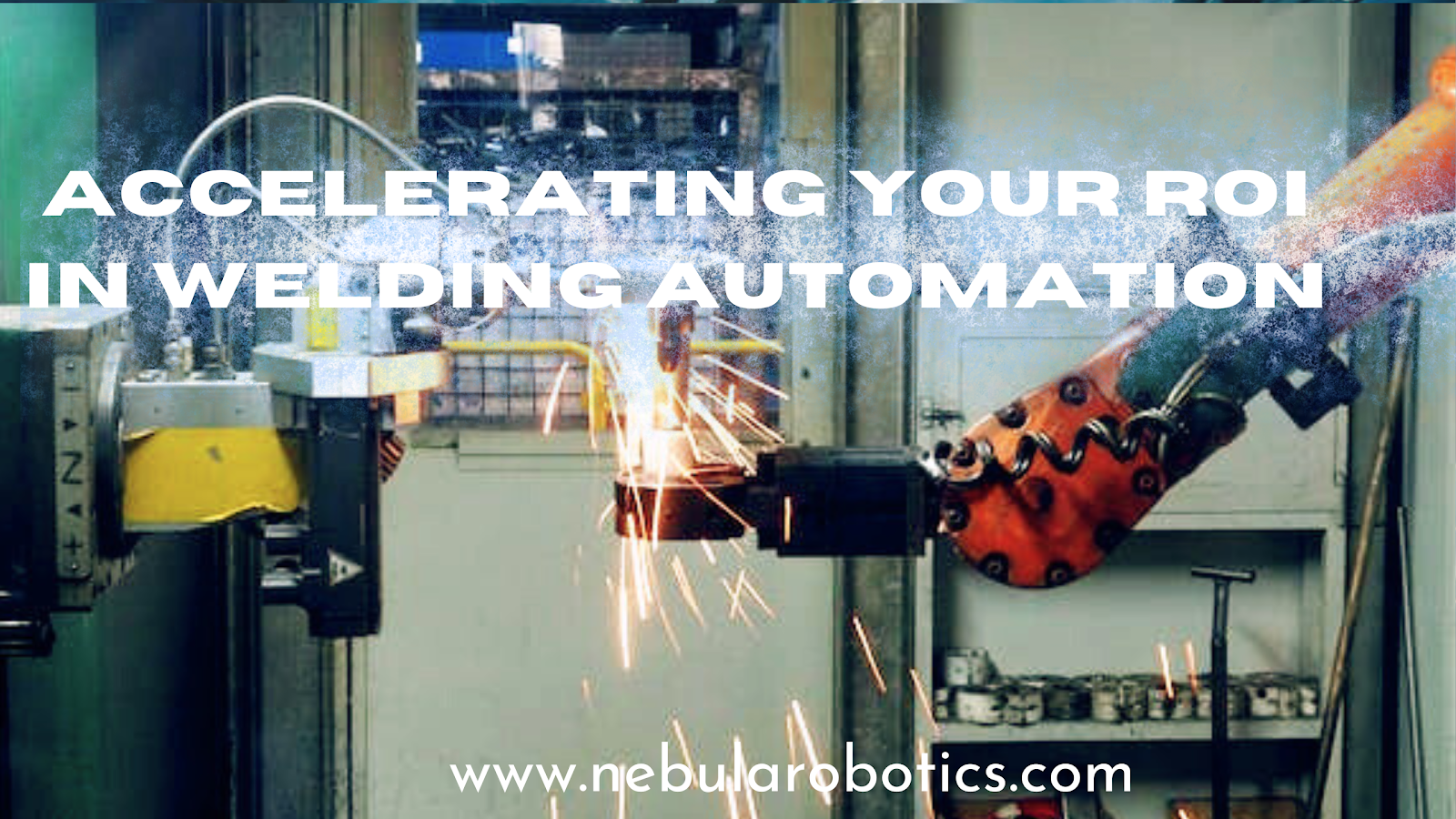
Click here to Checkout Nebula’s Weilding Robots!
Visit our website:
https://www.nebularobotics.com/
Connect to us on LinkedIn:
https://www.linkedin.com/company/nebularob
Email us and get answers to all your queries:
Email:
Phone:
(+91) 9137250668
Nebula’s YouTube page:
https://youtube.com/@nebularobotics7492