Force sensing and force control have become increasingly prominent in the field of robotics, although their utilization remains limited among existing robots. In this blog post, we will explore the history of force sensing and force control in robotics. But before delving into that, let's understand why force sensing is necessary for certain applications.
The historical progression of robotics sheds light on the initial purpose of robots and how they have evolved over time. In the 1970s, industrial robots were predominantly employed for welding tasks, primarily in the automotive industry. Welding demands high repeatability, where the robot must execute the same motion repeatedly. However, welding does not require significant adaptability since the robot does not exert force on the welded parts.
Consequently, the early robots were designed to be exceptionally rigid, as repeatability was their paramount characteristic. Over the years, these designs were refined to optimize stiffness, resulting in unprecedented manufacturing precision and quality in robot joints. When new applications necessitated adaptability rather than rigidity, it became more convenient to employ a standard stiff robot equipped with a sensor at its end-effector or tool.
For instance, robots intended for assembly or finishing tasks were equipped with force sensors capable of continuously measuring contact forces. Algorithms were then employed to compensate for robot motion based on these force measurements.
Book your free session with us!
Initial Approaches to Force Sensing
The initial approaches to force control involved analog force-torque sensors connected to digital acquisition cards within an external controller. Control algorithms would run on the controller, issuing position offsets to the robot to compensate for motion based on the sensor readings. This approach posed challenges when using standard industrial robots since their closed controllers required programming in dedicated programming languages, limiting its accessibility to experts.
Standardization
Gradually, industrial robot manufacturers adapted their controllers to facilitate easy retrofitting with force-torque sensors. Customers could purchase optional force control modules enabling force control on the robot, programmed through the standard programming language. This approach is widely employed by industrial robot integrators today, some of whom specialize in force-control applications. However, a substantial level of expertise is still required, as numerous parameters must be adjusted to achieve satisfactory results.
New Approaches
Modern robots are evolving to facilitate simplified deployment, especially in force-control applications that tend to be more complex. Moreover, contemporary robots, including collaborative robots (cobots), are built on open platforms that encourage third-party companies to develop components and software that are user-friendly.
For force control, this means that third-party force-torque sensors can now be easily installed on robots, and force control can be programmed using intuitive graphical user interfaces. This has unlocked new functionalities such as contact detection, simple force operations, and hand-guiding of the robot, which is particularly useful for teaching tasks.
While force-controlled trajectories have become simpler to implement, a certain level of expertise is still necessary to combine the appropriate instructions and set the parameters correctly.
Some robots now come equipped with force sensing as a default feature, either through a force-torque sensor at the wrist or torque sensors at each joint. Incorporating these sensors in each unit produced significantly reduces hardware costs and optimizes design by eliminating external sensor cables that can be prone to failure in production. This transformation also turns force control into a software-enabled capability of the robot, enabling more third-party developers to innovate and simplify cobot deployment further.
Another trend that enhances the ease of robot deployment is the emergence of application-specific force-control software. For example, dedicated software tailored to finishing applications can be configured using parameters relevant to the specific process, eliminating the need for extensive programming of complex robot-related concepts like singularities or frames. This application-specific software can also control other aspects of the process, such as activating the finishing tool or generating application-specific robot trajectories.
The Future of Force Control
We are currently experiencing an innovative phase in robotics, making it challenging to predict future developments for force control. If we had to identify a potential advancement, it could be the emergence of specialized robots for specific applications. While contemporary robots are embedded with an increasing number of sensors, they still utilize stiff joints optimized for repeatability, even when not required for every application. Constructing robots from the ground up for force control applications, such as finishing tasks, could result in improved performance, reduced costs, or both.
Nevertheless, surpassing the decades of refinement in current robot technologies may prove challenging. Only time will tell what the future holds for robotics and force control.
Nebula Robotics: Your Ultimate Automation Solution
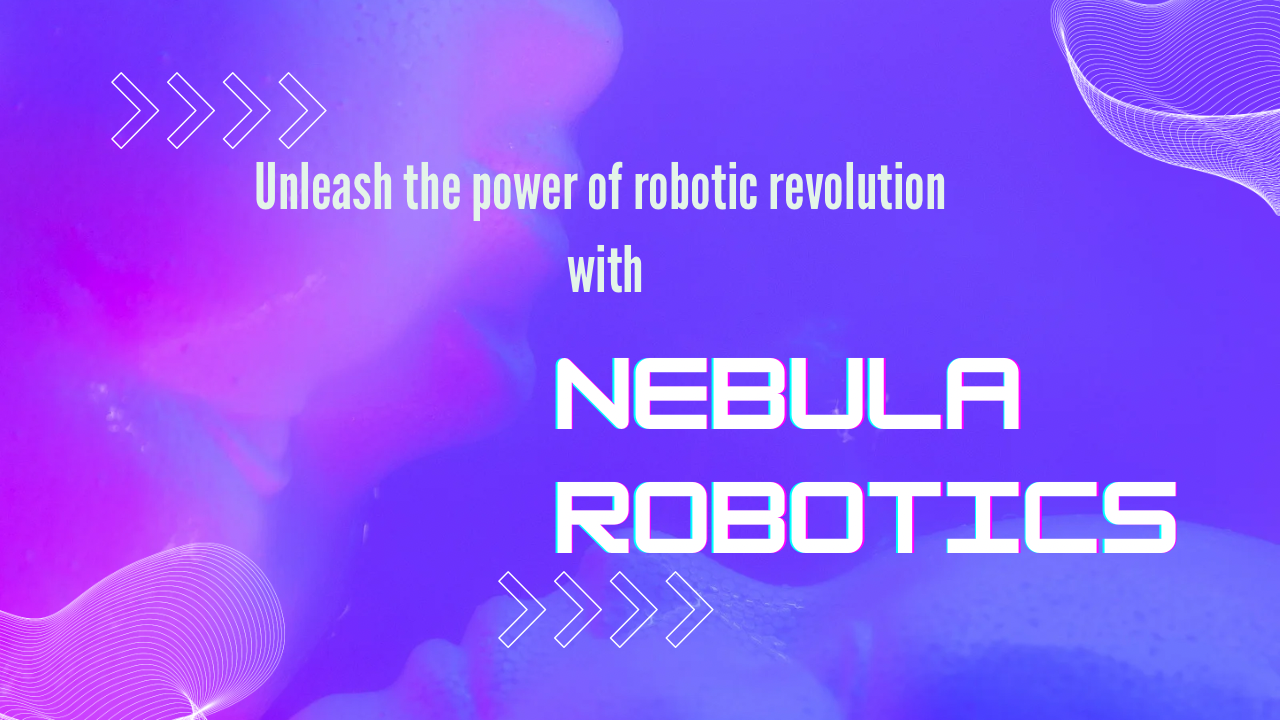
Say goodbye to automation problems with Nebula Robotics. Our cutting-edge technology offers the perfect solution to streamline your automation processes. From enhanced efficiency to improved precision, our robotics systems will revolutionize your operations. Experience the future of automation with Nebula Robotics.
Explore our ‘Zero Human Intervention’ in robotics
Contact us:
Email:
Phone:
(+91) 9137250668
Website:
https://www.nebularobotics.com/
LinkedIn:
https://www.linkedin.com/company/nebularobotics/