Robotic welding is a highly efficient method that automates the welding process, offering numerous advantages such as improved precision, enhanced safety, and reduced project completion time. This technology has gained significant popularity across various industries as a viable alternative to manual metal joining. By harnessing the power of automation, businesses can achieve their desired results swiftly and effectively.
Robotic welding process and Types
The field of welding demands a considerable level of expertise and specialized skills. However, the current number of professional welders falls short of meeting industry requirements. There’s a prediction that there will be a need for more than 375,000 welders by 2023 to fulfill consumer and company demands. To address this challenge, manufacturers can turn to robotic welding equipment as a supplementary solution.
Robotic welding systems automate the welding process, offering advantages such as increased precision, reduced material wastage, and faster operations. These machines are versatile and can adapt to various welding techniques, including arc welding, resistance welding, spot welding, TIG welding, and more.
ARC WELDING:
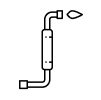
Arc welding is one of the most widely used forms of robotic welding. It involves the generation of an electric arc, which produces extremely high temperatures of up to 6,500 degrees Fahrenheit. The intense heat melts the metal, allowing the molten metal to join and solidify upon cooling. Arc welding is particularly suitable for projects requiring the accurate joining of large volumes of metal.
RESISTANCE WELDING:
Robotic welding systems can employ resistance welding for projects that require heat treatment or cost reduction. In this process, an electric current passes between two metal bases, creating a pool of molten metal that fuses the metal pieces together.
SPOT WELDING:
In cases where certain materials are resistant to electrical currents, such as in the automotive industry for assembling vehicle bodies, robotic welders utilize spot welding. This variation of resistance welding enables the connection of thin metal sheets at specific points.
TIG WELDING:
For robot welding applications demanding high precision, TIG welding, also known as gas tungsten arc welding (GTAW), is utilized. This technique involves an electric arc passing between a tungsten electrode and the metal base.
MIG WELDING:
Robotic welding commonly employs gas metal arc welding (GMAW) or MIG welding, which is a fast and straightforward method characterized by high deposition rates. The welding torch's heated tip continuously melts wire as it moves along, allowing molten metal to drip onto a base and connect it to another piece.
LASER WELDING:
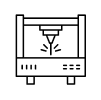
Laser welding is the preferred method for high-volume projects requiring exceptional accuracy in metal joining. It finds application in industries such as jewelry and medical component manufacturing, where small parts need precise welding.
PLASMA WELDING:
Among the various welding techniques, plasma welding offers the greatest flexibility. The operator can easily adjust the gas flow rate and temperature, allowing for versatile welding applications.
https://drive.google.com/file/d/1p_vK-8OnDZai4qmTzZ3JPffsqTPsv53c/view?usp=drivesdk
Working
The implementation of robotic welding requires certain adjustments compared to manual welding processes. Automation introduces additional tools and programming requirements that are not present in the traditional manual approach. Unlike human welders, robotic welders need to be programmed to perform their tasks effectively.
Robotic welding arms can be articulated, allowing movement in multiple planes, or rectilinear, moving in three dimensions. These arms receive the necessary wire through a wire feeder and utilize a high-heat torch to melt the metal and initiate the welding process. These robotic devices are designed to withstand the extreme temperatures involved in welding, ensuring the safety of human workers.
While robotic welders handle the physical welding tasks, certified human operators play a crucial role in overseeing the process. These operators are required to hold certification from organizations m, which certifies both manual welders and operators of robotic welding arms. The operators program the controller using a teach pendant, a device that allows them to set new programs, control arm movements, and adjust process parameters. The welding process is initiated using buttons on the operation box.
The robotic arm, equipped with a heating tool, melts the metal to join the desired pieces. A wire feeder is employed to supply additional metal wire to the arm and torch as needed. Between welds, the arm moves the torch to a cleaner to remove any metal splatters from the component, ensuring a clean surface before the next welding operation.
The integration of robotic welders aims to prioritize the protection of human workers, which is why these automated systems incorporate multiple safety features. Arc shields prevent the high-temperature arc from interacting with oxygen, minimizing potential hazards. Enclosed areas provide a protective barrier for operators, shielding them from the intense temperatures and bright light associated with welding operations.
Applications of Robotic Welding:
Robotic welding technology finds applications across a range of industries, catering to diverse needs such as metal fabrication and railway manufacturing. Regardless of the specific requirements, robotic welding offers a highly effective solution for complex metal projects.
RAILWAY INDUSTRY:
The railway industry frequently deals with the production of numerous car units, often receiving repeat orders for similar rail cars in large quantities. For instance, metal bolsters that connect container cars' ends are in high demand. Robotic welding technology can greatly assist rail companies in efficiently producing a variety of bolsters to meet these demands.
AUTOMOTIVE INDUSTRY:
The automotive industry relies on fast-paced production processes while adhering to complex safety regulations at the state and federal levels. Various car components, manufactured through methods like brake pressing or casting, require welding to join the parts together and ensure the overall structural integrity of the vehicle. Welding plays a critical role in areas such as motor assembly, water pump fabrication, and the secure fastening of metal components in car manufacturing.
FABRICATION INDUSTRY:
The metal fabrication sector stands to benefit significantly from the adoption of robotic welding technologies. Fabrication companies often handle multiple projects simultaneously, and robotic welding can enhance their productivity by enabling the completion of a higher volume of tasks. Whether it involves marine equipment or scissor lifts, welding serves as a reliable solution for successfully executing both one-off and ongoing projects across various industries.
Robotic welding proves invaluable in meeting the demands of industries seeking efficient and precise metal fabrication processes. Its versatility and ability to handle complex projects make it a preferred choice for businesses operating in sectors ranging from railway manufacturing to automotive production and beyond.
What the Future holds
Robotic welding, although currently representing a small fraction of welding projects, is poised for significant growth in the industry due to emerging technologies. Future innovations will make welding robots more user-friendly, interoperable with other machines, and increasingly popular.
MIND-CONTROLLED WELDING ROBOTS:
Researchers at the University of Illinois Urbana-Champaign have developed a prototype cap that translates brain waves into commands for a robotic welding arm. This technology has the potential to reduce the training required for manual welders to transition into robotic operators. Instead of relying on traditional programming methods, operators can simply wear the cap, review plans, and instruct the robot through thought commands. This advancement opens the possibility for robots to handle even smaller projects efficiently, eliminating the time-consuming programming process.
While commercial implementation of mind-controlled welding robots may still be a few years away, the success of the prototype paves the way for further development and refinement of this groundbreaking technology.
COLLABORATIVE ROBOTS:
Collaborative robots, designed with a user-friendly interface, are already being utilized in certain industries. These robots are equipped with sensors that enable them to gather information and adapt to changing situations, making them suitable for working alongside humans. Traditionally, industrial robots required extensive programming and occupied significant space, making them less feasible for smaller businesses. However, engineers have been developing more robust and cost-effective collaborative robots that can work harmoniously with human welders in industrial settings. This integration reduces conversion costs and provides substantial savings when combining robotics with other technologies. Collaborative robots have the potential to augment the work of human welders, leading to increased efficiency and productivity in manual welding operations.
A GROWING MARKET:
The transportation and automotive industries are actively embracing technological advancements to enhance productivity, with robotic welding playing a pivotal role in their operations. As global demand for automobiles continues to rise, these sectors are under pressure to increase production rates. Consequently, the welding industry is projected to reach a valuation of over $11 million by 2028, with a compound annual growth rate of 14.5% from 2021 to 2028. The need for accelerated vehicle manufacturing calls for investments in machinery, including robotic welding arms, to improve the speed and precision of the assembly process.
In summary, the future of robotic welding looks promising, driven by innovations such as mind-controlled welding robots and collaborative robots. These advancements will facilitate easier operation, seamless integration with other machines, and widespread adoption in various industries. With the transportation and automotive sectors leading the way, the welding industry is poised for substantial growth in the coming years.
Explore the revolution with Nebula Robotics:
We are pleased to present our comprehensive one-stop solution for all your metal fabrication and metalworking needs. Our range of services includes robotic welding, among various other offerings. Whether you have a specific project in mind or require assistance with a broader scope of metalworking requirements, we are here to provide you with expert solutions. To learn more about our robotic welding services or explore our comprehensive one-stop-shop offerings, we invite you to get in touch with us today.
Contact us:
Email:
Phone:
(+91) 9137250668