Screw assembly automation can greatly improve efficiency and productivity on assembly lines. However, there are several mistakes that companies should avoid when implementing screw assembly automation. By steering clear of these pitfalls, you can ensure a successful and smooth automation process.
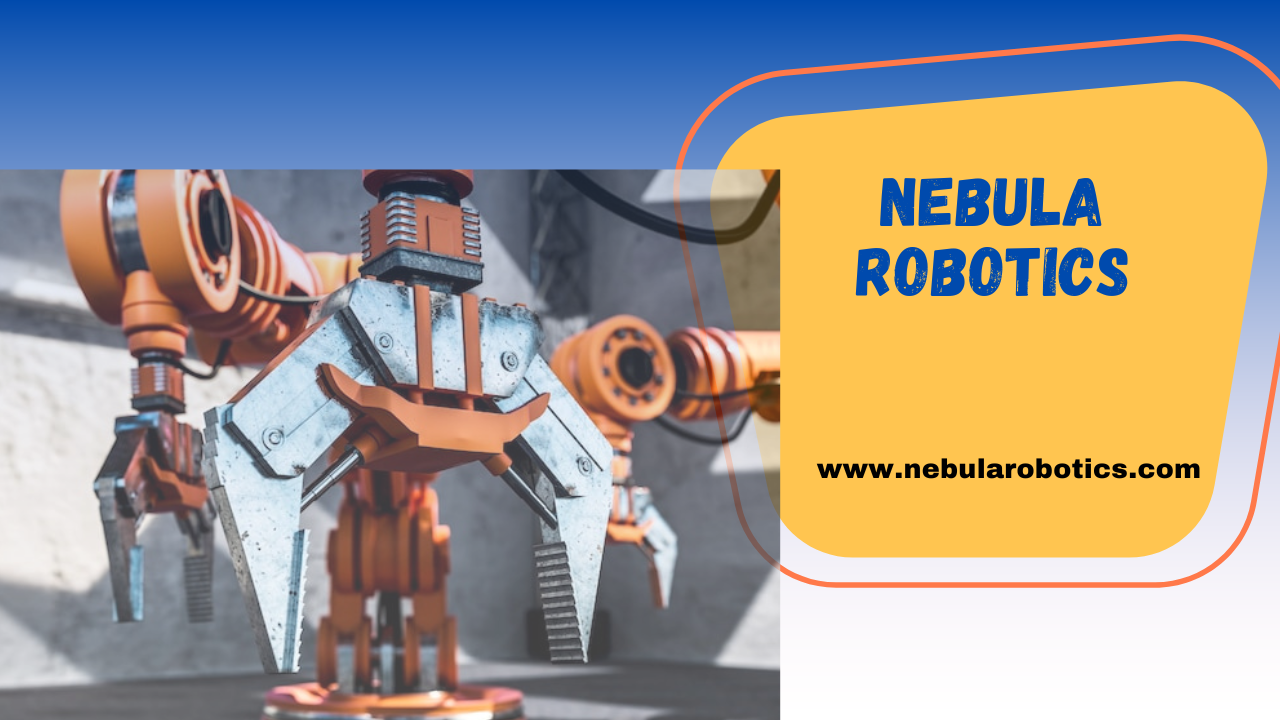
Checkout Nebula’s Efficient Robots !
Here are the top 7 mistakes to avoid in screw assembly automation:
Overcomplicating the automation:
Avoid attempting to automate complex tasks right from the start. It's better to start with a simple application and gradually build on that success. Overloading the automation system with too many tasks can lead to inefficiencies and increased complexity.
Incorrect sizing of the robot and accessories:
Choosing the right-sized robot and accessories is crucial for a successful automation project. Consider factors such as load, orientation, speed, travel, precision, and environment (LOSTPED) to accurately assess the requirements of your screw assembly task. Using the wrong-sized equipment can lead to subpar performance and decreased efficiency.
Neglecting to involve the team:
One common mistake is failing to involve the assembly team in the decision-making process. Including your team from the beginning fosters a sense of ownership and prevents mistrust. The expertise and insights of your team members can contribute to a more successful deployment.
Selecting incompatible end effectors:
Not all end effectors are suitable for all types of screws. Avoid assuming compatibility and make sure to choose the right end effector for your specific screws. Magnetic screwdriving tools, for example, work with ferromagnetic screws, while non-ferromagnetic screws may require vacuum-based tools or alternative solutions.
Using inadequate torque for high torque screws: Torque is a critical factor in screw assembly automation. Ensure that your chosen automation solution can provide sufficient torque for your specific screws. High torque screws, commonly found in industries like automotive or aerospace, require specialized systems that can meet their torque requirements.
Failing to account for space limitations:
When components are closely packed together on the workpiece, it can pose challenges for automation. Lack of space restricts the robot's movement and complicates the deployment process. It's important to have enough clearance around the fastening area to allow the robot to maneuver easily.
Automating low-impact or overly complex tasks:
Choose fastening tasks that offer high impact and are relatively simple to deploy. Automating tasks that have little impact on overall processes or tasks that are overly complex can lead to difficulties and a lack of return on investment. Focus on tasks that provide significant value and are feasible to automate.
By avoiding these mistakes, you can maximize the benefits of screw assembly automation and create a more efficient assembly line. Careful planning, proper equipment selection, and involving your team can contribute to a successful automation project.
Remember, partnering with an experienced automation provider can greatly simplify the implementation process. Nebula Robotics offers guidance, training, and ongoing support to ensure a successful deployment of screw assembly automation.
By following these steps, you can lay a solid foundation for your first screw assembly automation project and unlock the benefits of increased productivity, improved quality, and reduced labor.
Trust us with your automation projects!