Palletizing is a commonplace task in modern companies, particularly in the manufacturing sector where products need to be packed onto pallets for shipping. However, relying on manual palletizing can often prove to be a drain on valuable resources.
Manual palletizing is time-consuming, diverting workers' attention from more critical tasks. Improving the efficiency of the palletizing process can be challenging without clear guidance. Additionally, with limited resources and a shortage of skilled manual labor in many regions, continuing manual palletizing practices is likely to result in a waste of valuable resources.
Numerous customer experiences reveal the struggle of workers juggling multiple tasks simultaneously, including manual palletizing. This leads to reduced productivity across all tasks as employees attempt to manage various responsibilities.
To address these challenges and optimize productivity, it is highly recommended for companies to transition away from manual palletizing and embrace automation. Automated palletizing solutions, such as robotic systems, offer significant advantages. They improve efficiency, consistency, and precision in the palletizing process, relieving the burden on human resources and increasing overall productivity.
By adopting automated palletizing, businesses can make better use of their limited resources, streamline operations, and enhance efficiency in their production workflows. The shift from manual palletizing to automation enables companies to allocate their workforce more strategically, ensuring that each task is performed efficiently and effectively.
Reframing Palletizing as an Intermediate Task
When considering the task of palletizing, it becomes evident that it is an intermediate step rather than a core job function within the manufacturing process. As a manufacturer, the primary goal is to create products that reach customers promptly and efficiently.
In an ideal scenario, products would seamlessly transition from production to customer without any additional intermediate steps. However, due to the realities of the physical world and the need for logistics, tasks such as packaging and palletizing become necessary.
Value-added tasks are defined as those for which customers are willing to pay. Palletizing, in most cases, is not perceived as a value-added task. Given the choice between two equally excellent products, customers are unlikely to opt for the one that charges extra for the products being placed on a pallet.
Manual palletizing involves the labor-intensive process of manually placing items on a pallet. This non-value-added task is both challenging and time-consuming, making it an inefficient approach.
To enhance operational efficiency, it is crucial to streamline intermediate tasks like palletizing. Implementing automation solutions, such as robotic palletizing systems, offers a way to optimize this process. By automating palletizing, manufacturers can reduce labor-intensive efforts, increase efficiency, and allocate resources to more value-added activities within their operations.
In summary, recognizing palletizing as an intermediate task and seeking ways to automate it can contribute to a more efficient production process, reduced labor burden, and improved overall operational performance.
Addressing Inefficiencies in Manual Palletizing: The Role of Consistency
The inefficiency of manual palletizing is a common observation in manufacturing environments. Often, this inefficiency can be attributed to the lack of consistency in the palletizing operation.
Many companies experience inconsistent and varying volumes of product supply for palletizing. If a person were to wait for each box to arrive individually, a significant amount of time would be spent waiting rather than efficiently stacking boxes onto the pallet.
To mitigate idle time and keep workers productive, companies often assign multiple tasks to the palletizing operator. This may involve dividing their time between earlier packaging tasks and palletizing. While this approach keeps the person occupied, it can significantly reduce the efficiency of both tasks.
To understand the origins of this inefficiency, it is valuable to consider the waste introduced by manual palletizing:
- Waiting time: Waiting for individual items to arrive for palletizing leads to unproductive downtime and inefficient use of resources.
- Motion waste: The need for palletizing operators to move between different tasks and locations adds unnecessary motion, contributing to reduced efficiency.
- Overprocessing: Assigning the same operator multiple tasks can result in overprocessing, where excessive effort and time are invested in non-value-added activities.
To address these inefficiencies, companies can explore automated palletizing solutions. Robotic palletizing systems offer consistent performance, high-speed operation, and the ability to handle varying product volumes efficiently. By automating the palletizing process, businesses can eliminate waiting time, reduce motion waste, and optimize resource allocation.
Identifying Wastes in Manual Palletizing: Efficiency and Improvement Opportunities
When it comes to manual palletizing, several wastes can arise, negatively impacting efficiency and productivity. These wastes are aligned with the principles of Lean manufacturing. Let's explore the five key wastes associated with manual palletizing:
Waiting waste:
Manual palletizing often involves waiting time for the arrival of individual items or boxes to be placed on the pallet. This waiting waste leads to idle time for the palletizing operator and hampers overall productivity.
Motion waste:
Excessive and unnecessary movement is a common waste in manual palletizing. Palletizing operators may need to repeatedly walk back and forth between different locations, such as the end of a conveyor and the pallet, increasing the potential for errors and wasting time.
Overprocessing waste:
Overprocessing occurs when additional efforts, beyond what is necessary, are invested in a task. In the case of manual palletizing, this waste can manifest when the operator spends excessive time arranging boxes on the pallet or performing unnecessary actions that do not add value to the final outcome.
Defects waste:
Manual palletizing is prone to human errors, such as misaligned or improperly stacked boxes. These defects not only compromise the integrity of the load but also lead to rework, delays, and potential damage during transportation.
Underutilization of talent waste:
Assigning skilled workers to manual palletizing tasks may result in underutilization of their skills and expertise. It can hinder their ability to contribute to higher-value tasks or process improvements within the production workflow.
Addressing these wastes requires a shift from manual palletizing to automated solutions. Implementing robotic palletizing systems allows for improved efficiency, reduced waiting and motion waste, enhanced precision, and the opportunity to leverage skilled workers for more value-added activities.
By minimizing these wastes, businesses can optimize their palletizing processes, increase productivity, and improve overall operational effectiveness.
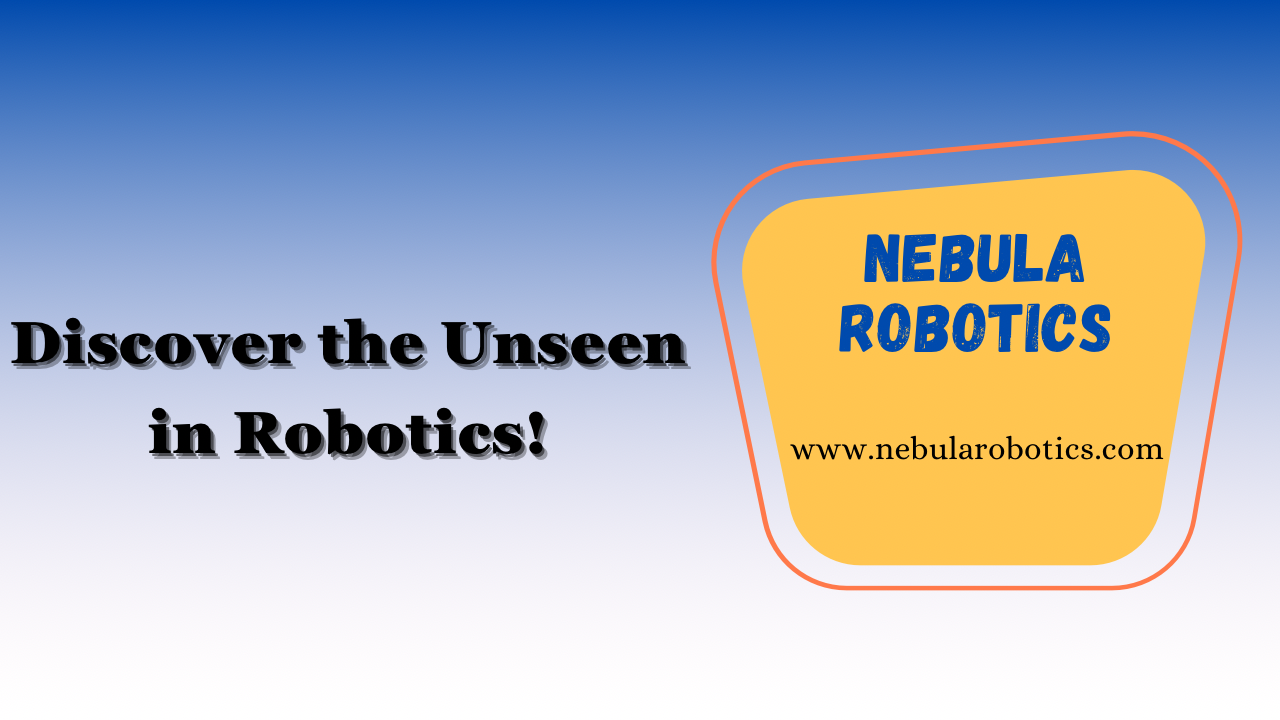
Meet the Palletizing Solution
Nebula Robotics' cobot palletizing solution offers an accessible and efficient alternative to manual palletizing, enabling companies to optimize their palletizing operations, improve productivity, and make better use of their human workforce. By embracing this technology, businesses can reduce waste, enhance efficiency, and achieve a more streamlined and cost-effective palletizing process.
Explore our ‘Zero Human Intervention’ in robotics
Want to get your Palletizing problems solved?
Contact us:
Email:
Phone:
(+91) 9137250668
Website:
https://www.nebularobotics.com/
LinkedIn:
https://www.linkedin.com/company/nebularobotics/