Avoiding cable mishaps and ensuring optimal functionality in robots necessitates effective cable management. With the intricate and diverse movements of robots, cable organization may appear daunting. However, by employing the right strategies, you can safeguard your cables and extend their lifespan.
Recognizing the significance of cable management is crucial when working with robots. While it may seem catastrophic for a cable to be torn apart by a robot, there are subtler yet equally problematic situations. Even imperceptible damage to a cable can lead to erratic robot behavior, posing challenges that are difficult to troubleshoot in real-time.
To mitigate such risks, adopting a proactive approach to robot cable management is essential. Waiting until an incident occurs is not an option, as autonomous robots can swiftly damage cables before the issue is even detected. By implementing effective cable management practices, you can not only prevent cable-related complications but also ensure uninterrupted robot performance.
Cables: Lifelines of Your Robot - Ensuring Reliability and Safety
Cables can be likened to the lifelines of your robot, as they play a crucial role in maintaining its proper functioning. When these lifelines are intact and in good condition, the robot operates smoothly as intended. However, any damage to these cables can jeopardize the robot's performance, leading to erratic movements that pose risks to both the robot itself and those working in its vicinity.
In the realm of robot cable management, it's important to recognize the three main types of cables typically found on robots:
- Power cables: These cables supply the necessary electricity to power the robot and its associated tools, enabling their operation.
- Communication cables: Serving as conduits for digital or analog signals, communication cables facilitate the exchange of information between the robot and its tools, enabling seamless coordination.
- Pipes: Certain tools employed by robots, such as pneumatic or hydraulic grippers, rely on additional fuel sources. Pneumatic pipes deliver compressed air, while hydraulic systems employ fluid-carrying pipes. These pipes ensure the proper functioning of specific tools.
Compromised cables within any of these categories can significantly impact your production processes. When such an issue arises, it becomes imperative to halt the robot, conduct thorough testing to identify the problem, and initiate the necessary repairs. These actions consume valuable time and may disrupt overall productivity.
Hence, prioritizing effective cable management is crucial for ensuring the reliability, safety, and uninterrupted performance of your robot system.
Identifying the Culprits: 6 Common Causes of Cable Failure in Robots
Cable failures can significantly impact the operation of your robot system, and it is essential to understand the six common causes behind such failures:
Loss of continuity: Over time, the electrical continuity of a cable can be compromised due to accumulated small misuses. Troubleshooting such issues can be challenging since the effects are often intermittent, making it difficult to pinpoint the exact problem.
Insulation damage: When the electrical insulation surrounding a cable is damaged, it can result in short-circuiting between two or more wires, potentially disrupting the flow of electricity.
Corkscrewing: This type of failure occurs when the entire cable becomes twisted and deformed. Cables constructed in layers are more susceptible to corkscrewing compared to bundled cables.
Jacket abrasion: The outer jacket of a cable can wear through, exposing the underlying cables or shielding. This not only reduces the cable's resistance to environmental elements like dust or oil but also increases its vulnerability to electrical interference.
Jacket swelling/cracking: Exposing a cable to inappropriate oils, chemicals, or extreme temperatures can cause the jacket to swell and crack. This compromises the protective properties of the jacket, potentially leading to wire damage.
Shielding losses/EMI: Compromised electrical shielding in a cable can result in Electromagnetic Interference (EMI), which negatively affects cable performance. This interference can disrupt signals and lead to degraded operation.
The effects of these cable failures on robot operation can vary. In some cases, there may be no immediate noticeable impact as long as the cable's continuity is maintained. However, working with damaged cables is akin to a ticking time bomb. Eventually, the cable is likely to fail, leading to potential disruptions and malfunctions in the robot system.
Therefore, addressing cable failures promptly and ensuring proactive cable management is vital to maintaining optimal robot performance and preventing future complications.
Introducing Nebula Robotics Expert Robot Cable Management Solutions
At Nebula Robotics, we understand the critical role that cable management plays in ensuring the longevity, performance, and safety of robotic systems. With our expertise in robotics and commitment to innovation, we offer comprehensive solutions for effective robot cable management.
Customized Cable Routing: We recognize that every robot setup is unique, with varying cable requirements. Our team of experts works closely with you to design and implement customized cable routing solutions tailored to your specific robot configuration. By carefully organizing and securing cables, we optimize their placement to minimize stress, prevent tangling, and reduce the risk of damage during robot movements.
Cable Protection and Retention: We provide a range of cable protection measures to safeguard your robot cables from external factors that can cause abrasion, impact, or environmental damage. From cable carriers and conduits to cable tracks and strain relief devices, we ensure that your cables are well-protected, reducing the risk of insulation damage or jacket wear.
Cable Management Accessories: Nebula Robotics offers a comprehensive selection of cable management accessories designed to enhance the overall organization and tidiness of your robot cables.
Our product range includes cable clips, cable ties, cable wraps, and cable brackets, among others. These accessories enable secure cable routing, prevent cable entanglement, and facilitate easy maintenance and troubleshooting.
Cable Testing and Maintenance: To ensure the continued reliability and performance of your robot cables, we provide comprehensive cable testing and maintenance services. Our technicians utilize advanced testing equipment to assess cable continuity, insulation integrity, and shielding effectiveness. By identifying potential issues early on, we help you mitigate cable failures and proactively address any underlying problems.
Future-Proof Solutions: As technology evolves, so do the demands on robot cable management. We stay at the forefront of industry trends and advancements. We continually explore innovative solutions and incorporate the latest cable management techniques into our offerings. By partnering with us, you can benefit from future-proof solutions that keep your robot cables well-organized and protected for years to come.
Trust Nebula Robotics for Expert Robot Cable Management
With our dedication to quality, attention to detail, and customer-centric approach, Nebula Robotics is your trusted partner for all your robot cable management needs. From initial design and installation to ongoing maintenance and support, we ensure that your robot cables are organized, protected, and optimized for peak performance.
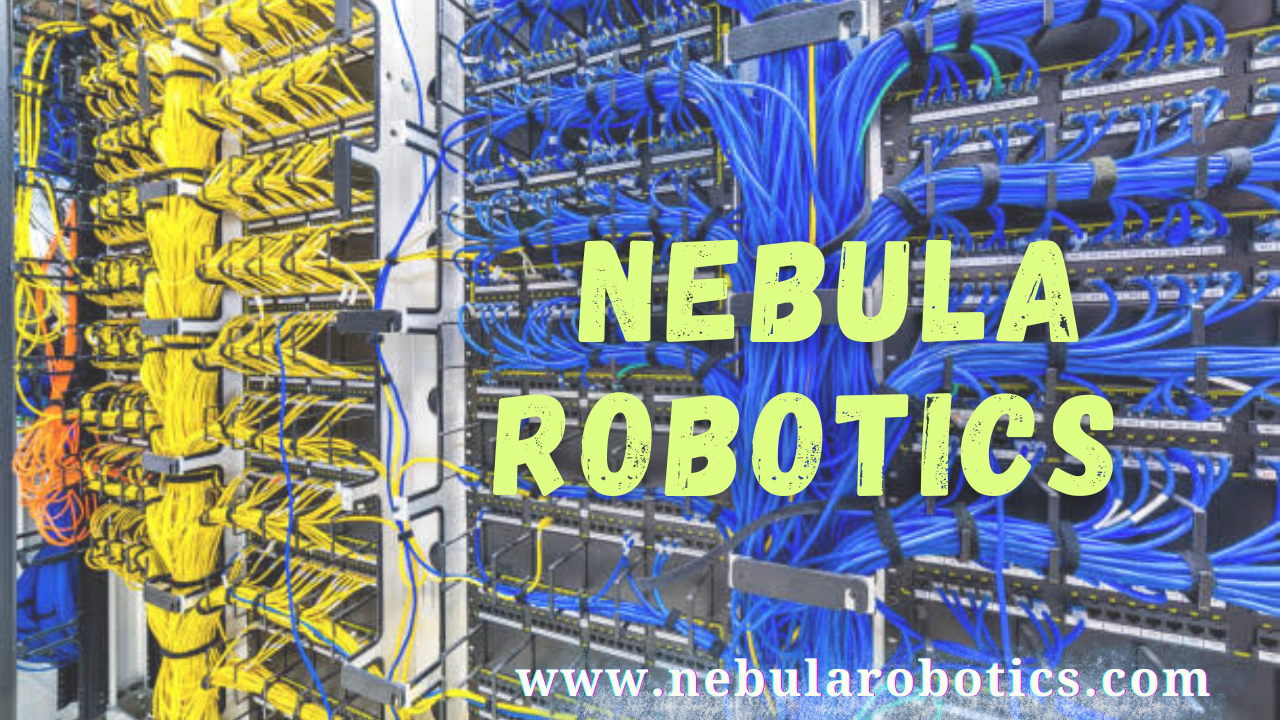
Experience the difference of superior cable management with us.
Contact us:
Email:
Phone:
(+91) 9137250668
Website:
https://www.nebularobotics.com/
LinkedIn:
https://www.linkedin.com/company/nebularobotics/