Worker injuries can significantly harm a company's production, morale, and financial security. While sanding and polishing may appear to be simple operations at first appearance, they are not without risk. In reality, these power tool finishing operations account for a sizable amount of lost workdays from accidents. Robotic finishing, on the other hand, is a revolutionary technology that can assist avoid operator accidents and thus cut down on lost workdays. In this post, we'll look at seven ways that utilizing robotic finishing technology might improve worker safety.
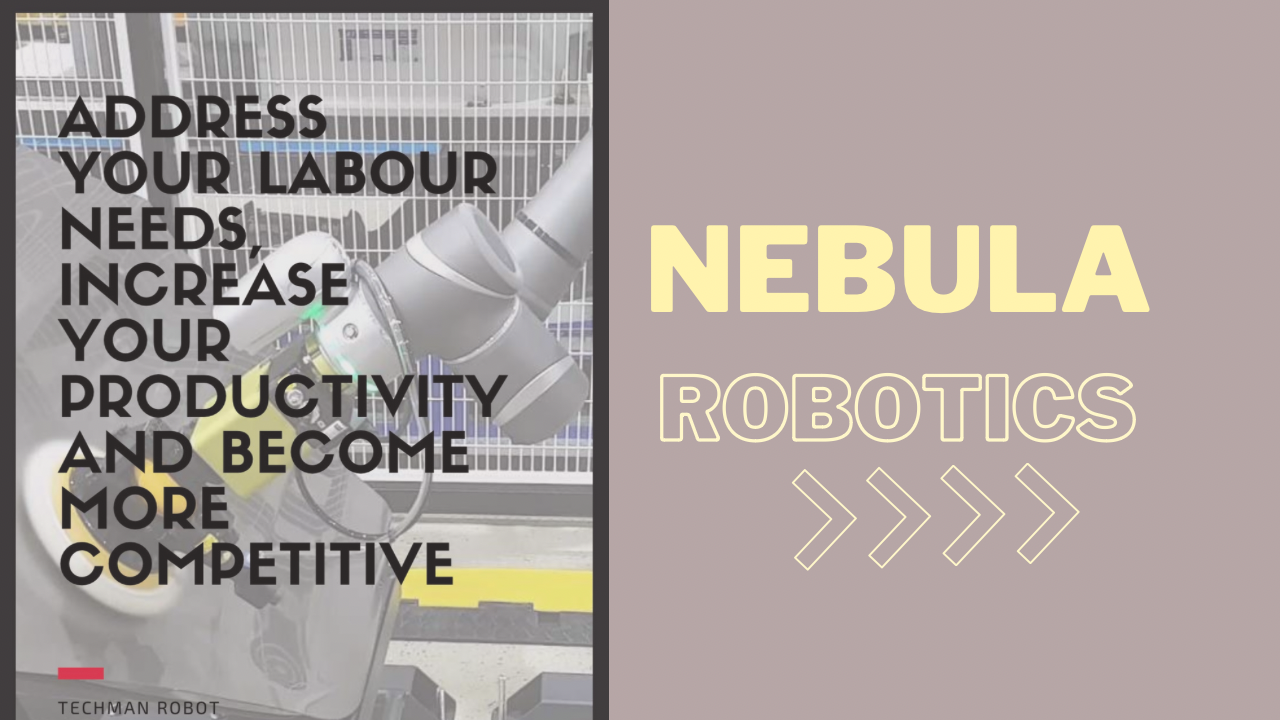
Let’s look at 7 key points in this blog post :
Using robotic finishing
A highly effective way to eliminate workers injury ixs to avoid doing manual sanding and polishing. Programming a robot to complete the sanding and polishing task is a great idea instead of hands.
Robotic finishing offers two major advantages :
- Productivity of a worker increases in this case. Workers can move their focus and skills to more engaging value-added tasks.
- Safety of worker is ensured creating a safer and trustworthy work environment.
However it is important to note that robotic finishing is not fit for every polishinh and sanding activity.
Until now, automated finishing solutions were beyond the reach of most businesses due to their costs and space requirements. The conventional CNC-like machines were pricey and took up a lot of floor area. Current advancements in automation sector have modified the landscape, making robotic finishing more accessible and adaptable to businesses of varying sizes and demands. These advancements allow companies to assimilate robotic systems into their manufacturing and production processes without incurring extremely high expenses or sizeable floor space usage.
Wearing the suitable PPE
One of the most evident and highly effective ways to alleviate potential harm during manual finishing is by applying the suitable Personal Protective Equipment (PPE).
It is one of the most crucial factor in ensuring the safety and well-being of workers in such hazardous tasks.
The major types of PPE that are vital for manual finishing include:
- Respiratory Protection: Sanding and finishing activities generate harmful dust particles, which can pose serious health risks, especially with prolonged exposure. Wearing proper respiratory protection, such as dust masks or respirators, becomes essential to safeguarding respiratory health.
- Eye Protection: During sanding, small particles or debris can easily be ejected from the machine and pose a threat to the eyes, even if the worker is wearing glasses. Eye protection, like safety goggles or face shields, is indispensable in preventing eye injuries.
- Hearing Protection: While many finishing machines produce relatively low noise levels, some louder ones can expose workers to potentially harmful noise. Utilizing appropriate hearing protection, such as earplugs or earmuffs, is crucial to avoid hearing damage.
- Foot Protection: General foot protection is a wise practice in manufacturing environments, including during manual finishing tasks. Wearing sturdy and closed-toe footwear helps prevent potential foot injuries from falling objects or machine-related hazards.
- Hand Protection: Sanding machines can cause skin burns, and unexpected tool movements may lead to cuts, scratches, or burns on the hands. Adequate hand protection, such as gloves designed for the specific task, provides a crucial barrier against such injuries.
Enhance work ergonomics
Poor ergonomics is one the main reasons behind these hazardous workplace injuries. Daily finishing tasks that are common can put a finishing operator at risk.
A crucial step in reducing these dangers is to address ergonomic concerns and improve workstation design. It is difficult to totally eliminate all potential risks involved with these duties, nevertheless, because of their manual nature.
Reduce Harmful Vibrations
People who have operated a power sander for longer than an hour at a time are familiar with the strange sensation of pins and needles in their hands following machine shutdown. When you undertake sanding procedures every day, this extended exposure to vibration might result in substantial harm, even though the sensation normally goes away gradually.
A reliable way to reduce this risk is to minimize the amount of time that the operators are performing sanding or polishing activities.
Ensuring that the workpiece is fixed
In the repetitive nature of sanding jobs, it's quite common to overlook securing the workpiece properly. Unlike precise and aggressive manufacturing tasks like machining, there's often a insight that incomplete workpiece fixation during sanding might not have significant consequences, even though we are familiar that it should be adequately secured.
However, avoiding to secure the workpiece poses serious dangers. The workpiece could unexpectedly shift or fall, potentially causing harm to the operator or others in the workplace.
Reducing Dust
Sanding and Polishing tasks produces dust that can be harmful to health. Along with PPE, extra measures should be taken to tackle this problem. Dust extraction can be beneficial in such cases.
Meet your Robotic Solution: Nebula Robotics!
Visit our website:
https://www.nebularobotics.com/
Connect to us on LinkedIn:
https://www.linkedin.com/company/nebularob
Email us and get answers to all your queries:
Email:
Phone:
(+91) 9137250668
Nebula’s YouTube page:
https://youtube.com/@nebularobotics7492