Improving Precision in Machine Vision Inspection
Firms today are using machine vision systems for production facility inspections, the emphasis has shifted away from simply having a machine vision inspection solution and toward assuring the highest accuracy and efficiency in your inspection system.
Machine vision inspection has considerably increased efficiency and production output for several manufacturers. Machine vision inspection, as opposed to human inspection, uses cameras to quickly evaluate images and make decisions on the acceptability of finished items and packaging. Unlike traditional sample procedures, machine vision systems can frequently inspect each individual product and package.
When used properly, machine vision systems can do inspections at a rate that is hundreds of times faster than human capabilities. However, if the inspection equipment is not properly calibrated or has other flaws, inferior accuracy might pose significant challenges. Reduced inspection rates or inaccurate results may result in lower production throughput and significant financial losses for the producer.
Ways to improve vision inspection
Choose adequate lighting:
Even the best cameras cannot capture clear images in the absence of adequate lighting. Depending on the circumstances, backlighting, bright field lighting, or a low-angle linear array may produce the best results. To make an informed selection, consult with your system integrator.
Adjust your lighting calibration:
Additional calibration may be required after you've determined the best lighting type. Adjust the frequency and wavelength of your lighting arrangement to reduce interference from the manufacturing environment or coatings on the products and materials used.
Filter the source of light:
Machine vision works best in consistent surroundings, which might be difficult to maintain throughout the day. Ambient light, changed production lines, and moving products can all have an impact on lighting conditions. Using a lens filter can help to reduce unwanted images.
Make use of the trigger range functionality:
Electrical noise in the manufacturing area can cause the inspection system to trigger incorrectly. This can interrupt analysis and result in incorrect product failures. Such instances can be avoided by using a trigger range function.
Integrate artificial intelligence technologies:
Artificial intelligence and embedded technologies are becoming more accessible to a wider range of manufacturers. AI can improve decision-making by intelligently analyzing large datasets and avoiding errors.
Improve part placement:
Acceptable components can fail inspection due to poor placement. Incorporating more precise tooling to secure items during inspection can improve machine vision assessment accuracy.
Improve stability:
Equipment in manufacturing facilities is frequently subjected to noise and vibration, which can cause image blur. This blurring can cause unneeded failures and demand additional inspections. Stability measures are being implemented.
Want the right vision inspection for your industrial purpose?
Click here to checkout Nebula’s Guide on Computer Vision & AI for Industrial Automation
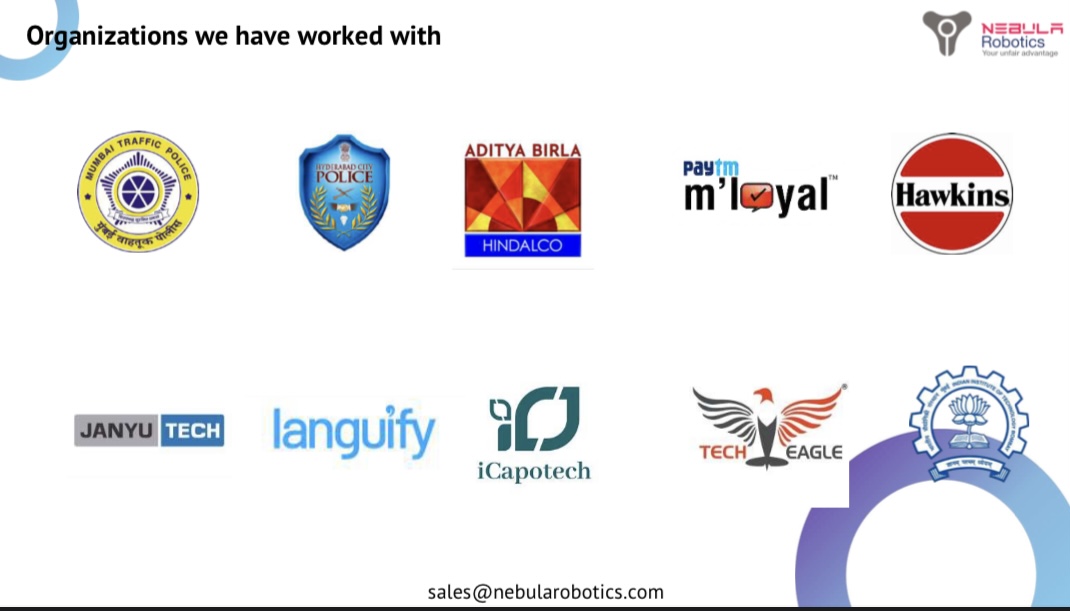