Harnessing Automation : Re imagining the art of welding
Welders are crucial to the survival of our interconnected world, and their importance cannot be stressed. Welding employment are predicted to grow dramatically in the following decade, highlighting their critical contribution to worldwide societies.
Welding has a long history, reaching back to roughly 3000 BCE, when pressure or forge welding was practiced. Metals were heated and skilfully hammered together in these ancient procedures to establish a tight bond. The contemporary concept of welding, as we know it now, arose in the late nineteenth century with the introduction of electrical welding equipment.
Welding: an art
Welding is more than just a metal connection; it requires both technical expertise and imagination. Creating delicate metal welds necessitates trained perception and exceptional manual dexterity. It takes years of devotion and experience to master this art and win recognition from peers and companies. Welding is a true art form, requiring both imagination and devotion.
Nonetheless, obstacles abound. Welders are exposed to high temperatures, molten materials, and poisonous gases due to the dangerous nature of the job. Repetitive activities, such as long straight welds or dozens of similar ones, are also part of the profession. Predictably, less young people are interested in welding, which has an influence on skill development. Welding, like other trades, has a somewhat tarnished reputation, and its sophisticated expertise is undervalued.
As a result, there is a skills deficit, which is worsened by the retiring welding workforce. It is becoming increasingly difficult to meet the rising demand for welding. Welders play an important part in several industries today, including heavy industry, metal fabrication, energy, appliance manufacture, infrastructure, building, and heating, ventilation, and air conditioning. Welder shortages might jeopardize critical projects such as installing district heating lines or erecting wind turbines.
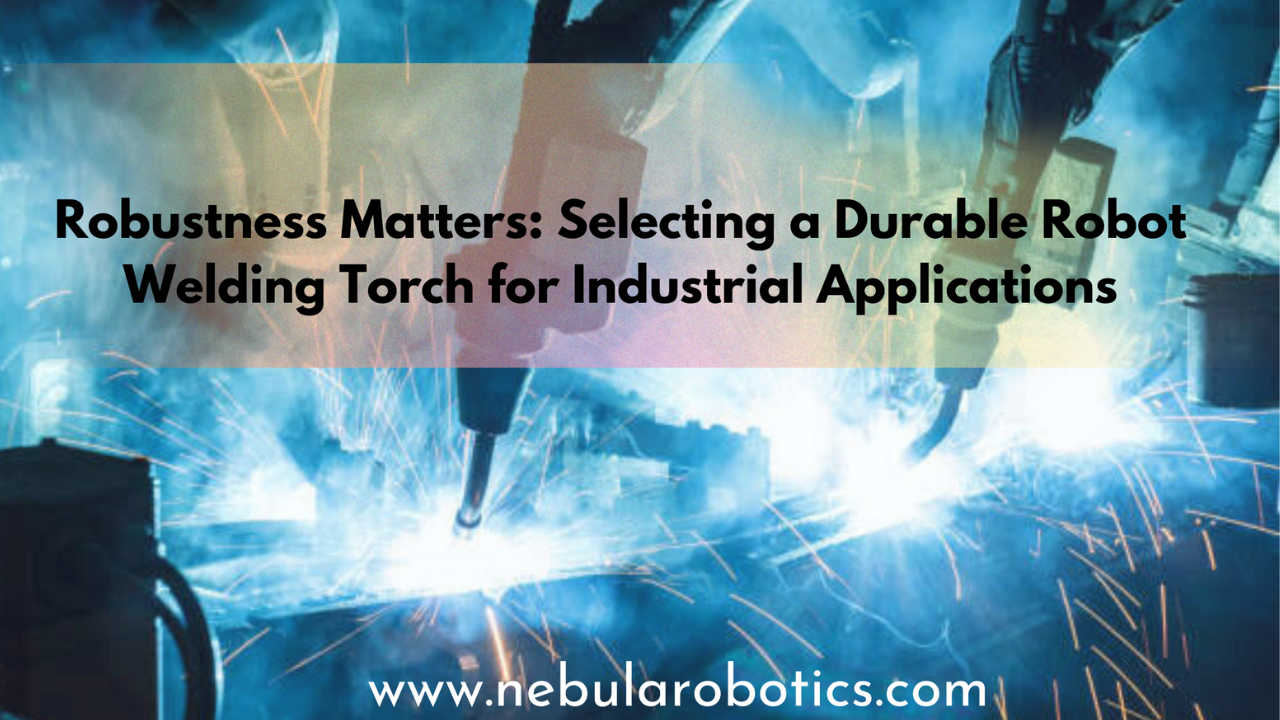
Imagine if welders had better tools to increase their job happiness and working circumstances. This is where robotics enters the picture.
The best approach
Collaborative automation, in which welders collaborate with tiny robots, has the ability to address the welding skills deficit.
This latest form of automation allows the age-old trade to subcontract monotonous welding to robots. As a result, human energy may be directed toward the creation of delicate and aesthetic metal items, a domain reserved for skilled craftspeople. Welding goes beyond conventional production limits, requiring creativity and skill in producing high-quality outcomes. In this context, a collaboration between qualified human welders and robots provides significant benefits by increasing value and providing safer work environments.
Trust us with your welding solutions
Nebula’s Cobots have the potential to alleviate labor shortages in the welding industry by reducing physical demands and repetitive operations. This allows seasoned welders to advance their careers while also attracting younger enthusiasts who are drawn to the possibilities afforded by collaborative technology.