Guide to Robotic Grippers
The era of robotic revolution is full of changes and transformations. Robotics has not only changed the landscape of work but has been yielding profitable results for years now.
Human hands are prone to risks and injuries while doing work, whereas robotic grippers are designed to perform such operations.
With human workers, there are chances of errors and with robotic grippers the chances are none, so a robotic gripper is what fits in well for performing such tasks.
The Robot arms also consist of the elbow and wrist. At the end of the arm, we can find the grippers. Robotic grippers, also known as 'end-effectors' or manipulators,' are specialized devices that help robots handle items in real-world circumstances.
Robotic grippers exist in a wide variety of designs and functions. Some have two or three fingers and resemble human hands, while others have a more robotic claw-like appearance. Grippers with large suction cups, soft round ball grippers, and magnetized tips are available. The variety of gripper types is a direct result of the diverse range of objects handled by robots, such as textiles, electrical components, and automobile parts.
They are critical in industries such as manufacturing, logistics, agriculture, healthcare, and space exploration because they allow robots to grip and move items with precision and adaptability. As sensor technology and artificial intelligence progress, these grippers will be able to alter their grasp depending on real-time feedback, increasing their usefulness in a variety of applications.
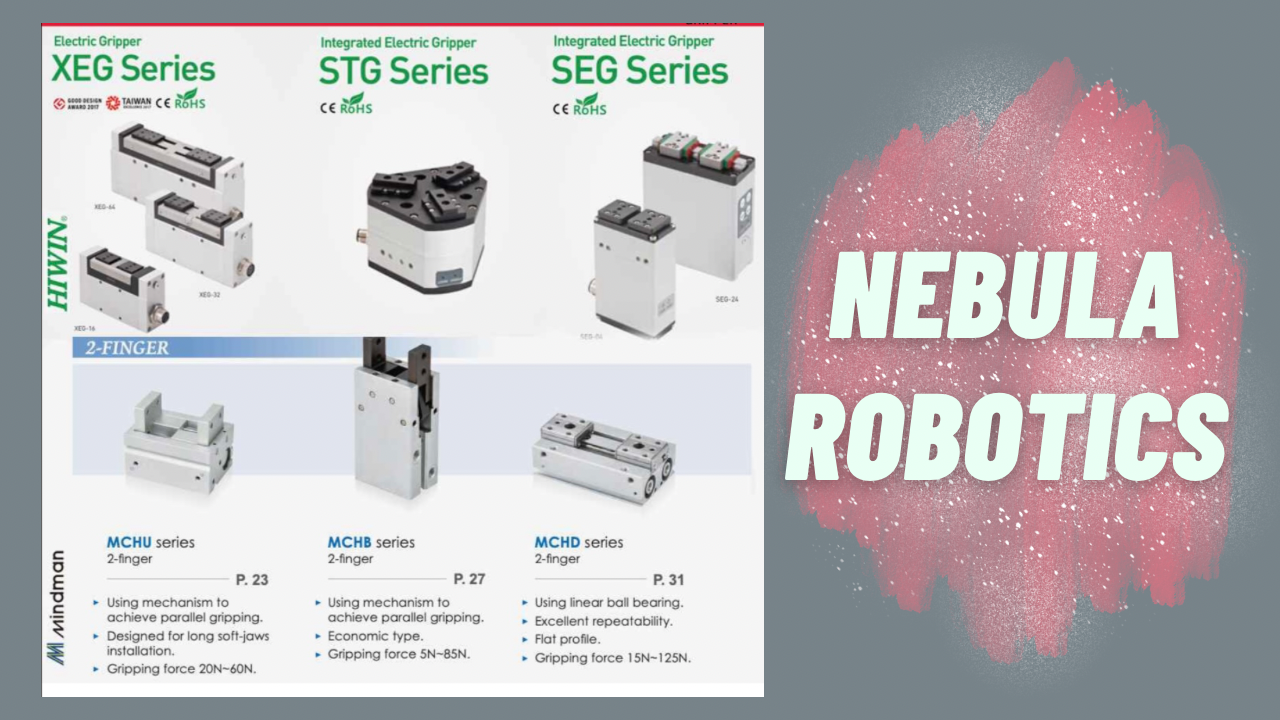
Points to consider for selecting the right robotic gripper
Payload : The term "payload" describes the total weight that a robot arm, including the gripper and the arm itself, can support. Robots are likewise restricted in their ability to lift weight, much like human arms and hands have certain lifting limits. To guarantee effective and secure operations, it is vital to consider both the gripper's and the robotic arm's payload capacities when choosing a robotic gripper.
Application : The most appropriate gripper for your automation is generally determined by the individual application in mind. Consider the products you'll be handling, such as tiny batch items, sensitive electrical components, or large boxes for assembly or palletizing. Different gripper properties may be required for each application.
If you're working with fragile products, for example, a gripper with a gentle touch is vital to avoid damage. A gripper with a solid grasp, on the other hand, would be better ideal for activities demanding strength.
Furthermore, certain applications, such as handling food, may necessitate grippers that are certified as food safe in order to comply with safety laws.
Types of Robotic Grippers
Servo-electric grippers
They are equipped with an electric motor and a controller. The controller generates signals specifying the necessary force, position, or speed for the robot's operation. The gripper then receives these signals and executes the desired motion using its motor.
In some cases, servo-electric grippers come with extra features that allow them to communicate with the control system. For instance, when the gripper picks up a part, it can send this information back to the control system. This valuable feedback helps reduce errors on the production line, improving overall efficiency and accuracy in the automation process.
Two-finger grippers
For smaller operations, two-finger/jaw grippers are commonly employed in manufacturing. The end-effector is made up of two parallel jaws with flat sides that open and close with force, securely clamping onto the part to preserve stability. These grippers, however, have limits when dealing with unusual forms and sizes since they lack adaptation in such situations.
Three-finger/jaw grippers
They have three fingers or jaws that come together to grasp an item firmly in the center. They are especially well-suited for handling round or cylindrical objects with accuracy and stability.
Magnetic Grippers
Magnetic grippers, as the name indicates, utilize magnetized surfaces to grip and manipulate metal objects. Magnetic grippers, as opposed to typical grippers with fingers or jaws, rely on smooth magnetic surfaces to operate. They are extensively employed in sheet metal and automotive parts industries, particularly in assembly line procedures where efficient movement and manipulation of metal components is critical.
Vaccum Grippers
To lift, hold, and transfer things, vacuum grippers use the difference between internal gripper air pressure and exterior air pressure. Suction cups form the point of contact between the item and the robot gripper. Handling mixed product runs becomes simple by altering the size and shape of the suction cups. Some vacuum grippers require an external air supply, whilst others include built-in vacuum generators that are powered by the robot's electrical supply, removing the need for an external air source.
Click here to checkout Nebula’s Robots!
Visit our website:
https://www.nebularobotics.com/
Connect to us on LinkedIn:
https://www.linkedin.com/company/nebularob
Email us and get answers to all your queries:
Email:
Phone:
(+91) 9137250668
Nebula’s YouTube page:
https://youtube.com/@nebularobotics7492