Using a collaborative robot (cobot) for palletizing jobs has various benefits, including streamlining your production operations and resulting in increased efficiency, productivity, and cost savings. You may achieve seamless workflow management and greatly increase output rates while lowering costs by implementing this robotic palletizing solution. Using such modern automation technology offers a smoother and more streamlined manufacturing process, which translates to enhanced overall performance and better outcomes for your company.
The importance of automation in the future of manufacturing is generally recognized. It has already proven useful in assisting firms all over the world in optimizing their operations, increasing production capacity, and navigating the obstacles created by a global labor shortage. While the advantages of automation are obvious, effectively adopting a robotic palletizing solution takes careful thought and preparation.
The tasks of production and technical managers are vast and complex, ranging from managing commodity prices and supply chains to fulfilling decreased delivery times and adjusting to changing consumer demands. The scarcity of trained personnel exacerbates these issues, making automation an enticing answer. Finding the time and resources to prepare for and incorporate robot-based automation might be difficult.
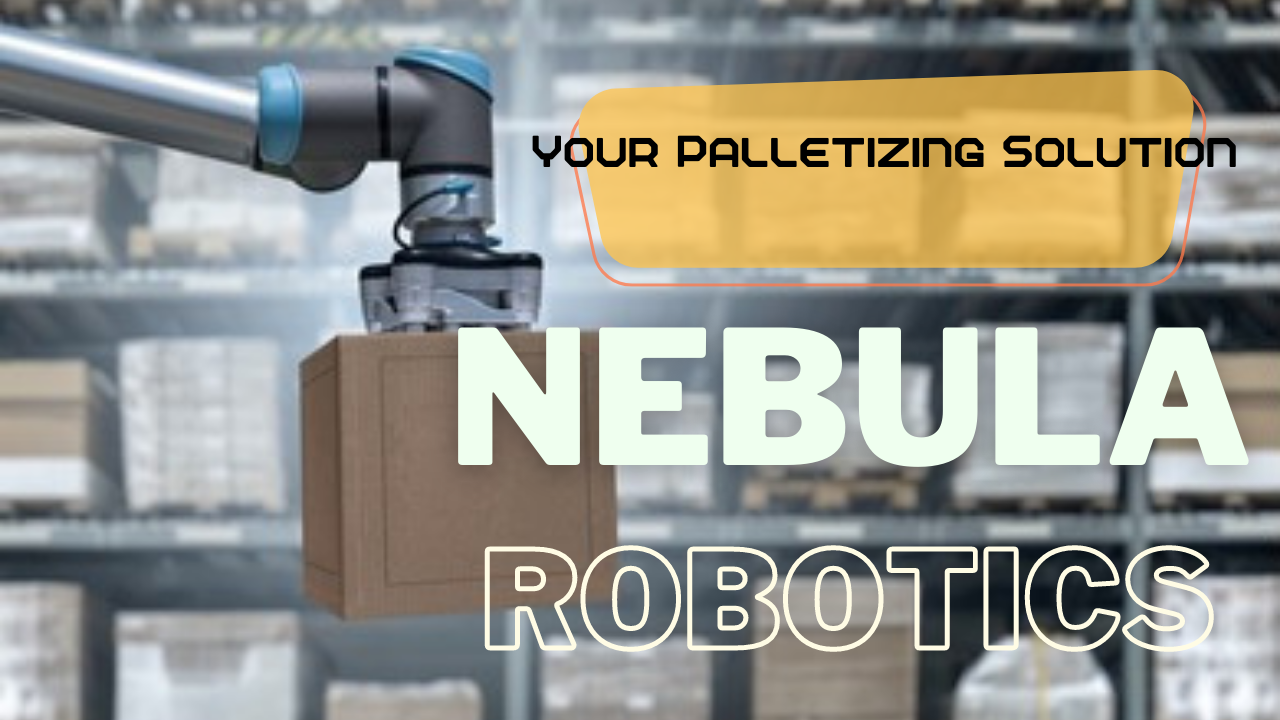
Understanding Payload
Choosing the best cobot model for your palletizing operations may appear simple, but it requires careful consideration of several important variables. You must first determine whether the chosen cobot can properly handle the weight of the packages and products to be handled, as well as the conveyor system's throughput. Understanding the payload requirements is critical, particularly if the cobot must manage numerous boxes at the same time, which may entail a larger payload capacity.
It is also critical to include the weight of the grippers in your calculations to ensure optimal performance. Ignoring this element could result in unexpected problems during operation.
Selecting the appropriate gripper
Your cobot's effectiveness is primarily reliant on its end effector, also known as the end-of-arm tooling or gripper. Choosing the right gripper is key to the success of your project, and there are numerous important factors to consider.
To begin, the type of packaging utilized, particularly whether it is wrinkled or lightweight cardboard, will determine the applicability of specific grippers. To ensure reliable and efficient palletizing, use a gripper that can handle the exact characteristics of your product's packaging.
Second, consider the cobot's work pace as well as the nature of its working environment. If your robotic palletizing system will be operating at or near its payload limitations for extended periods of time each day, choosing lighter grippers can assist reduce wear.
Prioritizing Safety
When incorporating a cobot into your business, safety must be prioritized. Before installing the cobot, it is critical to do a thorough risk assessment. Pay great attention to worker and machine safety, especially when there is close contact with sharp edges or when handling big payloads at rapid speeds. You may create a safe and secure work environment for everyone participating in the robotic palletizing process by addressing potential hazards through comprehensive safety evaluations.
Checkout Nebula’s Zero Intervention Robots!
Visit our website:
https://www.nebularobotics.com/
Connect to us on LinkedIn:
https://www.linkedin.com/company/nebularob
Email us and get answers to all your queries:
Email:
Phone:
(+91) 9137250668
Nebula’s YouTube page:
https://youtube.com/@nebularobotics7492