Improving efficiency in logistics through the implementation of robotics is a growing trend in the industry. While it may not be immediately apparent how robots can integrate into logistics processes, their presence is increasingly becoming prominent. Just like other companies in the market, you too can reap the benefits of efficiency gains by leveraging robotic automation effectively.
When considering the suitability of robotics in logistics, several applications come to mind. Robots can be utilized for tasks such as automated picking and packing in warehouses, autonomous material handling and transportation, inventory management, sorting and distribution, and even last-mile delivery. These applications can help streamline operations, reduce errors, enhance speed and accuracy, and ultimately improve overall efficiency.
Measuring the efficiency improvements introduced by a robot can be done in various ways. Key performance indicators (KPIs) such as cycle time, throughput, order accuracy, labor productivity, and resource utilization can be monitored before and after implementing robotics. By comparing these metrics, you can assess the impact of robotic systems on your logistics operations
.
Robotics for logistics efficiency
Logistics efficiency is characterized by the optimal transportation, storage, and distribution of materials, while minimizing waste. The goal is to reduce wasteful processes, which translates to less budget, energy, time, and natural resources being wasted.
In the realm of logistics, eight types of waste can impact processes. These include transportation waste, which refers to unnecessary movement of goods; waiting waste, which occurs when materials or resources are idle; overproduction waste, where more goods are produced than needed; defects waste, involving faulty or damaged products; inventory waste, which arises from excessive stock levels; movement waste, indicating unnecessary or inefficient movements within operations; overprocessing waste, which involves using more resources than necessary for a task; and underutilization of human potential waste, which occurs when employees' skills and abilities are not fully utilized.
By identifying and addressing these types of waste, logistics operations can achieve higher levels of efficiency. This involves streamlining transportation routes, reducing idle time, optimizing production levels, improving product quality control, implementing effective inventory management systems, minimizing unnecessary movements, optimizing processes to eliminate unnecessary steps, and maximizing the potential of human resources.
Efficiency in logistics is ultimately about finding ways to minimize waste across the entire supply chain. By focusing on these waste types and implementing strategies to mitigate them, businesses can enhance their overall efficiency, leading to cost savings, improved sustainability, and increased customer satisfaction.
Enhancing Logistics Efficiency through Robotic Automation
In logistics, many tasks are characterized as dull and repetitive, such as the manual movement of boxes onto pallets. These types of tasks can lead to inefficiencies, as human workers tend to perform worse over extended shifts when their jobs lack stimulation and fulfillment. However, since palletizing is a fundamental step in logistics processes, it cannot be eliminated entirely.
Robotic automation provides a solution to automate these repetitive tasks. By deploying robots to handle palletizing, human workers can focus on more challenging and rewarding aspects of logistics jobs. This includes activities like responding to last-minute changes, troubleshooting breakdowns, and addressing nonstandard requirements that require human expertise and adaptability.
When robots are used efficiently, they contribute to waste reduction in the overall process. By automating repetitive tasks, robots minimize errors and enhance productivity. They can work tirelessly without fatigue, maintaining a consistent level of performance throughout extended shifts. This helps to improve the efficiency of the entire logistics process.
By leveraging robots to handle repetitive and mundane tasks, logistics operations can optimize the allocation of human resources. This ensures that human workers are engaged in more meaningful and value-added activities, where their skills and problem-solving abilities can be effectively utilized. As a result, the overall efficiency of the logistics process is enhanced, leading to improved productivity, reduced waste, and potentially higher levels of job satisfaction for human workers.
In summary, by employing robots efficiently in logistics, businesses can automate repetitive tasks, allowing human workers to focus on more critical and rewarding aspects of their jobs. This optimization leads to waste reduction and ultimately improves the overall efficiency of the logistics process.
Leveraging Robot Application Kits to Enhance Logistics Efficiency
Robotics offers several applications that can be effectively utilized in logistics operations. Here are three common tasks where robots can be deployed to enhance efficiency:
Palletizing: Palletizing is a widely performed task in logistics that involves stacking boxes or items onto pallets. This repetitive action can potentially lead to injuries for human workers over time. Robots excel in palletizing as they offer flexibility and can be easily programmed to handle various box sizes and shapes. They provide a reliable and consistent solution to automate this task efficiently.
Pick and Place: Many logistics tasks revolve around moving objects from one location to another, such as packaging items into boxes or sorting and assembling orders. Robots are well-suited for pick and place operations. With their precision and consistency, robots can perform these tasks more reliably than human workers. Additionally, the simplicity of programming options allows for easy setup and adjustment to different item configurations.
Machine Tending: Certain logistics processes involve the use of semi-autonomous machines, such as labeling or wrapping equipment. Typically, human workers are responsible for feeding objects into these machines, which can be monotonous and add little value to the overall process. Machine tending robots can take over this task, improving the consistency and efficiency of the process. By automating machine tending, human workers can be freed up to focus on more complex and critical aspects of their roles.
By deploying robots for these specific tasks, logistics operations can streamline processes, reduce human error, enhance productivity, and ultimately improve overall efficiency. It is important to identify tasks that are best suited for automation while ensuring that human workers are allocated to roles where their skills and expertise are most valuable.
Measuring Efficiency Improvements after Implementing a Robot in Logistics
When assessing the impact of introducing a robot into logistics operations, it can be challenging to quantify efficiency directly. However, there are several key metrics that can be used to gauge the performance of a robot in a logistics setting:
- Shipping Time: This metric measures the speed at which items are shipped after being ordered. By comparing the shipping time before and after implementing the robot, you can assess if there is a reduction in the overall time it takes to process and dispatch orders.
- Perfect Order Rate: The perfect order metric calculates the percentage of orders that are shipped without any issues or errors. It helps determine the accuracy and quality of the order fulfillment process. Monitoring the perfect order rate before and after introducing the robot can indicate if the robot's involvement has improved order accuracy.
- Capacity Utilization: This metric evaluates how effectively the robot is utilized in comparison to its potential capacity. By analyzing the robot's usage and comparing it to its maximum capabilities, you can identify opportunities to optimize its deployment and maximize its efficiency.
- Cycles Completed: This metric measures the number of cycles or program executions that the robot performs within a specified time period. Tracking the cycles completed can provide insights into the robot's productivity and its ability to complete tasks efficiently.
- Wait Time: Wait time refers to the amount of time the robot spends waiting for other processes to occur, such as material supply or interaction with other systems. Monitoring and reducing the robot's wait time can help identify bottlenecks and optimize the overall process flow.
By analyzing these metrics before and after implementing a robot, you can gain a clearer understanding of the efficiency improvements introduced by the robotic application. These measurements provide valuable insights into the impact of the robot on key aspects of logistics operations, allowing for adjustments and optimization to further enhance efficiency.
Join us in our journey
Embarking on the journey to enhance the efficiency of your logistics operations with robotics may initially appear overwhelming. However, with Nebula Robotics, you can seamlessly get started and navigate the process effectively.
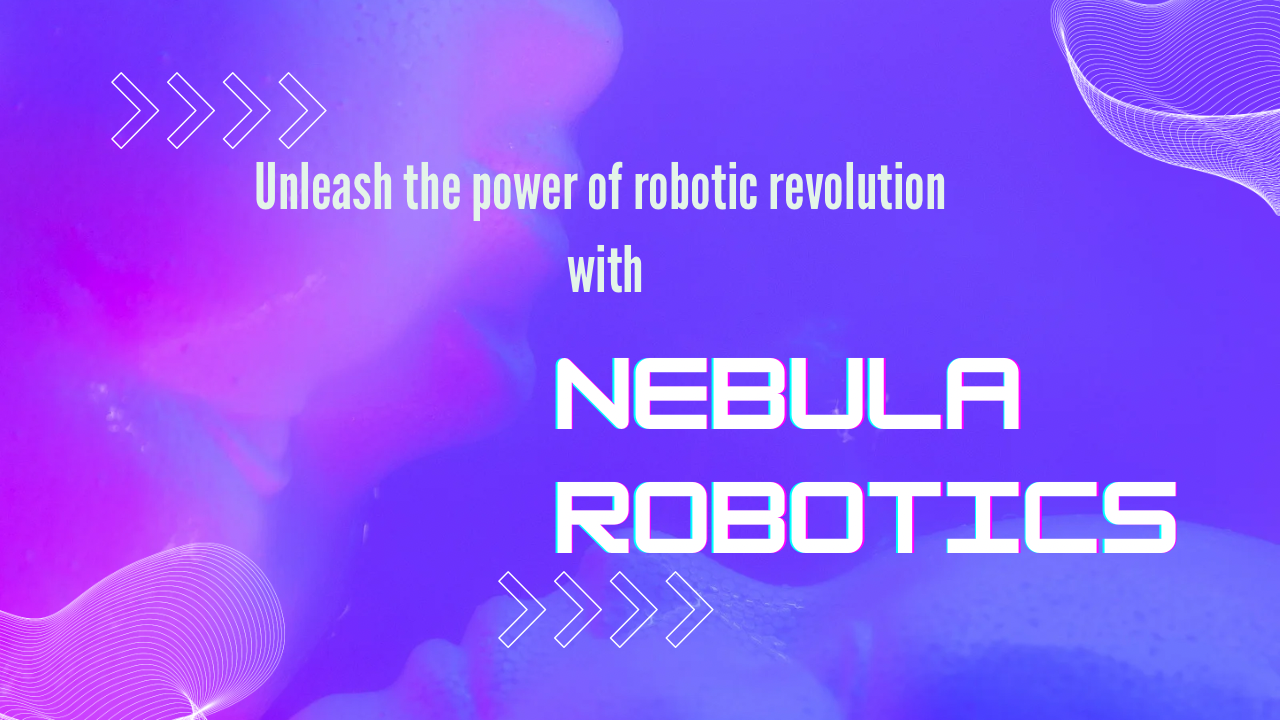
Assess your needs: Begin by identifying specific areas within your logistics operations that can benefit from automation. Determine which tasks are repetitive, time-consuming, or prone to errors, making them ideal candidates for robotic integration.
Explore Nebula Robotics solutions: Investigate the range of robotics solutions offered by Nebula Robotics. They provide application kits designed for common logistics tasks such as palletizing, pick and place, and machine tending. These preconfigured kits provide all the necessary components and software to deploy robots quickly and efficiently.
Evaluate compatibility: Evaluate the compatibility of Nebula Robotics solutions with your existing infrastructure and systems. Ensure that the robots can seamlessly integrate into your logistics operations without causing disruptions or requiring extensive modifications.
Plan implementation: Develop a comprehensive implementation plan in collaboration with Nebula Robotics experts. Consider factors such as robot placement, programming requirements, training needs, and safety considerations. Define clear goals and timelines for the deployment of robotics in your logistics operations.
Pilot testing and optimization: Start with a small-scale pilot project to test the efficacy of the chosen Nebula Robotics solution. Gather feedback, assess performance metrics, and make necessary adjustments to optimize the automation process.
Expand deployment: Based on the success of the pilot project, scale up the deployment of robotics in your logistics operations. Implement the robots in additional areas or gradually expand their usage to cover more tasks, unlocking further efficiency gains.
Continuous monitoring and improvement: Regularly monitor key performance indicators to measure the impact of robotics on logistics efficiency. Identify areas for improvement and fine-tune processes to maximize the benefits of robotic automation.
By following these steps with Nebula Robotics, you can confidently embark on your journey towards improving logistics efficiency through robotics, leveraging their expertise and tailored solutions to achieve optimal results.
Contact us:
Email:
Phone:
(+91) 9137250668
Website:
https://www.nebularobotics.com/
LinkedIn:
https://www.linkedin.com/company/nebularobotics/