While palletizing and depalletizing are often mentioned together in discussions about automation, it is important to recognize that these logistical tasks have distinct characteristics. Treating palletizing and depalletizing separately can lead to more effective decision-making when implementing automation in your production workflow.
By understanding the specific requirements of each task, you can better prepare your facility for robotic palletizing and maximize the benefits of your investment.
Here, we explore the similarities and differences between these two robotic endeavors.
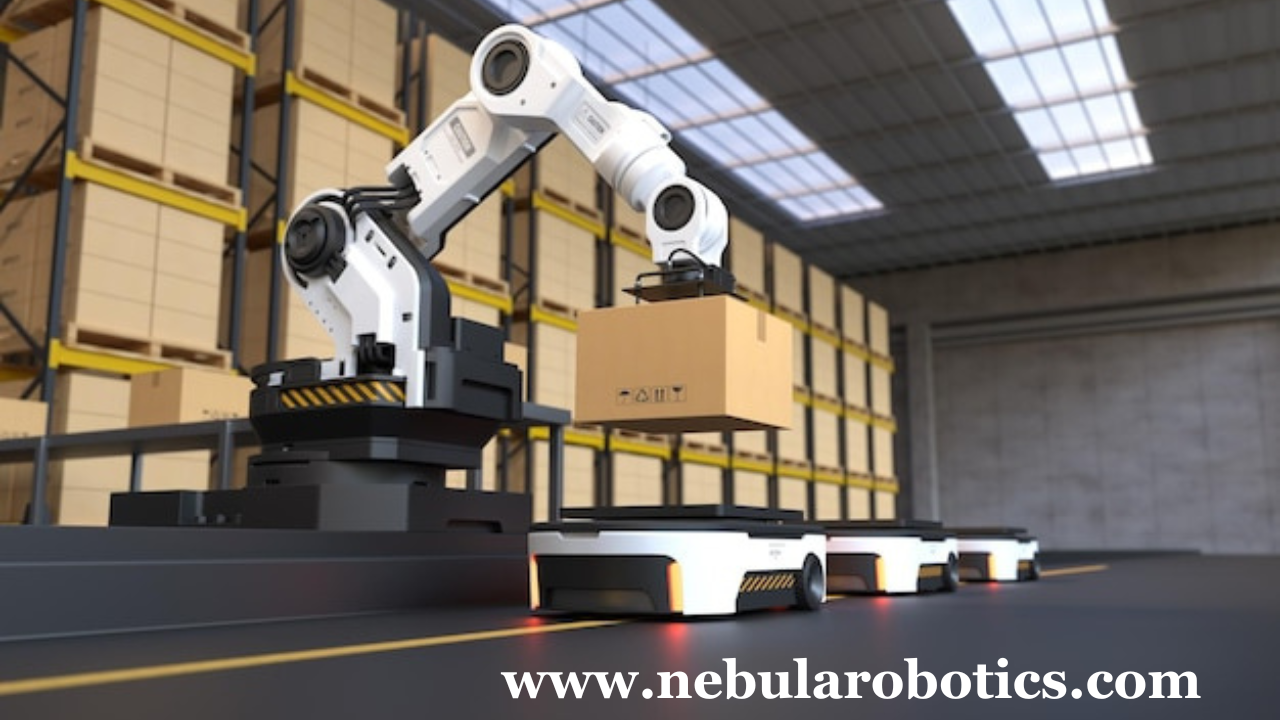
Explore our ‘Zero Human Intervention’ in robotics
Decoding Palletizing
Palletizing refers to the process of arranging or stacking items onto a pallet, typically made of wood, plastic, or metal, for the purpose of shipping or storage. It plays a crucial role in logistics by ensuring the protection and integrity of products during transportation. Palletizing is a widely adopted practice, with billions of pallets being utilized worldwide on a daily basis.
Traditionally, palletizing has been performed manually, where a worker takes packaged products from the production line and manually stacks them onto an empty pallet. However, in recent times, collaborative robots have gained popularity for automating the palletizing process. These robots offer advantages such as consistent performance and the potential to reduce the risk of injuries commonly associated with manual palletizing work.
By implementing robotic palletizing, businesses can achieve greater efficiency, precision, and safety in their operations. The use of robots can enhance productivity and enable companies to meet the demands of a rapidly evolving logistics landscape.
Decoding Depalletizing
Depalletizing involves the methodical extraction of boxes, bags, or other packaged items from a loaded pallet. It is commonly carried out as the initial step in a manufacturing process when raw materials arrive at a facility on pallets.
In comparison to palletizing, depalletizing tends to be a more intricate task. However, with appropriate configuration, robotic systems can effectively execute depalletizing operations. These automated systems offer advantages such as increased efficiency, precision, and reduced labor requirements.
Additionally, an associated task known as "repalletizing" can be performed. In repalletizing, items are taken off from one loaded pallet and transferred onto a second pallet for subsequent shipment or storage. This process is often implemented when reorganizing or optimizing the layout of goods within a warehouse or distribution center.
By employing robotic depalletizing and repalletizing solutions, businesses can streamline their material handling processes, minimize errors, and enhance overall operational productivity. These automation technologies contribute to the optimization of logistics operations and support the seamless flow of goods within a facility.
Recognizing the Similarities Between Palletizing and Depalletizing
It is valuable to refresh our understanding of the shared characteristics between palletizing and depalletizing tasks. These two logistical operations indeed exhibit several notable similarities:
Compatibility with the same robot: The Nebula Robotics Palletizing Solution, for instance, is capable of effectively handling both palletizing and depalletizing tasks.
Movement of items onto pallets: Both tasks involve the transfer of boxes, bags, or other items from a fixed point, such as the end of a conveyor, onto a pallet in a regularly arranged pattern.
Repetitive and monotonous nature: Palletizing and depalletizing tasks are repetitive and mundane, often regarded as undesirable manual labor.
Potential production bottleneck: These tasks can become bottlenecks in production facilities, particularly when palletizing operators are responsible for multiple roles.
Recognizing these similarities is crucial when considering the implementation of robotic solutions. They enable a consolidated approach where palletizing and depalletizing can be treated as interconnected operations.
Consequently, the deployment and integration efforts made for one task, such as palletizing, can be directly applied to the deployment of depalletizing, and vice versa. This streamlined approach facilitates efficient utilization of resources and simplifies the overall automation implementation process.
Highlighting the Distinctions Between Palletizing and Depalletizing
It is essential to acknowledge the significant differences between palletizing and depalletizing tasks, despite their outward similarities. These variations introduce unique challenges that may not arise—or may manifest differently—in one task compared to the other.
Consider the following key differences:
Unloading challenges:
Palletizing involves controlling the placement of items onto a pallet, whereas depalletizing entails unloading items from a pallet loaded by someone else. This introduces the potential for unexpected item positions or inconsistent item distribution on the pallet.
Items moved in transit:
Pallets often experience movement during transit, and inadequate load securing can result in shifting items. Depalletizing requires accounting for such movement to avoid errors during unloading.
Robot vision:
Adding robot vision is common in depalletizing applications to handle the uncertainty of unloading pallets. While it increases complexity, vision sensing enhances the system's flexibility in accommodating changes. Palletizing tasks often do not require additional vision sensing.
Different upstream and downstream processes:
Palletizing and depalletizing interact with distinct processes in the production workflow. Palletizing typically follows upstream packaging tasks like sealing, labeling, and case erecting. Depalletizing, on the other hand, usually occurs at the beginning of the workflow and involves tasks such as picking, sorting, and unpacking.
Location within the facility:
Palletizing and depalletizing robots often occupy different positions in the facility. It is important to place the robot in proximity to the upstream or downstream processes that precede or follow it in the workflow. Consideration must be given to the robot cell design and its integration into the facility layout, especially if the same robot is used for both tasks.
Understanding these differences is crucial for effective implementation of robotic automation. By addressing the unique challenges associated with each task, businesses can optimize their production workflows and maximize the benefits derived from robotic palletizing and depalletizing solutions.
Determining Your Facility's Palletizing and Depalletizing Needs
Assessing whether your facility requires a palletizing or depalletizing robot, or both, is crucial for making an informed decision. To determine the best palletizing solution for your specific situation, consider asking yourself the following questions:
Workflow bottlenecks:
Identify the points in your workflow where bottlenecks are most prevalent. Are they primarily at the beginning or the end of the process? This will help you understand which task (palletizing or depalletizing) is causing the greatest hindrance to your production efficiency.
Robot placement:
Decide on the optimal location within your facility to position the robot. Consider proximity to relevant upstream or downstream processes, as well as the availability of space and accessibility.
Single or multiple robots:
Evaluate whether you prefer to accomplish both palletizing and depalletizing tasks with a single robot or if it would be more efficient to have separate robots dedicated to each task. This decision may depend on factors such as workflow complexity, throughput requirements, and available resources.
Throughput considerations:
Estimate the expected throughput of products for each task. Understanding the volume of items to be palletized or depalletized will assist in determining the appropriate level of automation and the capacity required for efficient operations.
By addressing these questions, you can gain insights into your specific palletizing and depalletizing needs, enabling you to make informed choices about robot deployment, configuration, and integration. This will help optimize your production workflow, enhance efficiency, and maximize the benefits derived from automation technology.
Checkout Nebula’s Efficient Robots !
Contact us:
Email:
Phone:
(+91) 9137250668
Website:
https://www.nebularobotics.com/
LinkedIn:
https://www.linkedin.com/company/nebularobotics/